top of page
CWU C-Clamp Matchplate


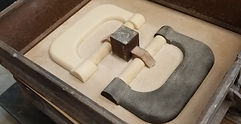
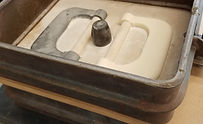

The goal was to design and manufacture a matchplate to be used by the Central Washington University (CWU) Engineering Department to cast C-clamps. These castings are produced in the University’s foundry and would be prepared as a secondary project for the department’s basic machining course. The design produced allows the C-clamps to be molded in a single pour for a full class of students, which is approximately sixteen (16). The desire was to achieve a matchplate result that was functional, yet allowed room and/or means to be easily modified or repaired, if needed. This was achieved through designing the C-clamps in a computer based model in the program Solidworks. By using Solidworks it allowed the imprints to be repeatedly modified and improved throughout the design process. This also allows future modifications to be easily made by subsequent students to the 3D design. This model was then converted into imprints for the matchplate and printed via a rapid prototyping system of a 3D printer. The results of these efforts yielded a functioning matchplate for testing. The results of the tests proved that it is capable of producing C-clamps effectively in enough quantity to supply the engineering department for the class project.
bottom of page