CWU C-Clamp Matchplate


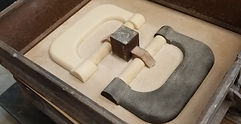
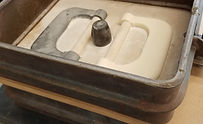

Construction
The device’s construction was broken down into two phases. The first phase was producing the imprints from the SolidWorks model and converting them into STL files. These files were used by the 3-D printer software Catalyst to print the require sets of imprints for the matchplate. A supplied set of particle boards were acquired from the University. Other supplies such as one inch diameter dowel rods, wood joining dowels, wood glue, and three-quarter by three-quarter inch wood blanks. Phase 2 of the project was constructing the matchplate for testing. To accomplish this wood dowels were rip cut in half on a band saw and sanded. A blank of wood was then placed in a wood lathe and hand turned to form the sprue well cap. The matchplate particle board was then drilled for the required datum's for the clamps, runners, and sprue well cap. All parts that required drilling for a dowel to be inserted and join the parts together and all parts were glued onto the matchplate board.


